اصول ساخت مخازن تحت فشار
مقدمه :
همانطور که مي دانيم مخازن تحت فشار از جمله تجهيزاتي هستند که نه تنها در شاخه نفت و پتروشيمي بلکه در اغلب صنايع اصلي نظير نيروگاه و حمل و نقل از کاربرد ويژه و قابل توجهي برخوردار بوده و از اينرو توجه به مقوله طراحي و ساخت آنها از اهميت ويژه اي برخوردار است .
تعاريف اوليه :
مخزن تحت فشار : بطور کلي هر مخزني که اختلاف فشار داخلي و خارجي آن برابر و يا بيشتر از 15 psi ( و کمتر از 3000 psi ) بوده , قطر داخلي آن از 6 in بيشتر باشد يک مخزن تحت فشار ناميده مي شود و شامل مقررات مندرج در ASME SEC. VIII DIV.1 ميگردد .
فشار و دماي کاري : فشار و دمايي است که مخزن تحت آنها به عملکرد عادي خود مي پردازد .
فشار طراحي ( UG-21 ) : فشاري است که جهت تعيين حداقل ضخامت مجاز براي اجزاء مختلف مخزن تحت فشار در نظر گرفته مي شود و معمولا 10% و يا 30 psi ( هر کدام که بزرگتر باشد) بيشتر از فشار عملياتي آن مي بشد . چنانچه مخزن داراي ارتفاع قابل توجهي باشد ( بيشتر از 10 متر ) لازم است که فشار استاتيکي ناشي از وزن سيال نيز به رقم مزبور اشافه گردد . در مورد مخازني که بطور معمول در شرايط خلاء کار مي کنند و يا اينکه امکان خلاء براي آنها محتمل است بايد طراحي با در نظر گرفتن پديده خلاء کامل صورت پذيرد .
درجه حرارت طراحي ( UG-20 ) : اين پارامتر نقش مهمي در طراحي يک مخزن تحت فشار ايفا مي کند چرا که مستقيما با مقدار تنش مجاز فلز بکار رفته در ساخت مخزن ارتباط دارد . به عنوان يک پيشنهاد مي توان براي مخازني که فعاليت آنها در محدوده قرار دارد بر اساس RATING فلنجهاي بکار رفته در آنها اقدام به تعيين درجه حرارت طراحي نمود چرا که حداکثر تنش مجاز براي فولادهاي کربني و کم آلياژ در محدوده فوق عمدتا ثابت است . براي مخازن با فولاد کربني که شرايط دمائي بهره برداري از آنها نزديک به محيط اطراف مي باشد تعيين حداقل درجه حرارت شکست ترد همواره وجود خواهد داشت . يادآوري ميشود که آيين نامه در هيچ حالتي اجازه استفاده از درجه حرارت بالاتر از 1000 براي فولادهاي کربني و 1200 براي فولادهاي کم آلياژ را نمي دهد .
حداکثر فشار کاري مجاز (UG-98 ) : فشاري است که تحت آن فشار ، ضعيفترين عضو مجموعه به نقطه نهائي تنش تسليم خود مي رسد و اين در حالي است که مخزن در شرايط ذيل قرار داشته باشد.
معمولا سازندگان مخازن تحت فشار مقدار M.A.W.P را با توجه به مقاومت عدسي و يا پوسته مخزن تخمين مي زنند و اجزاء کوچک مثل فلنج يا دريچه ها را مبناي محاسبه قرار نمي دهند .
بنابراين با توجه به تعريف اصلي MAWP خواهيم داشت :
MAWP < MAWP
فشار تست هيدرواستاتيک ( UG-99 ) : فشار اين تست 5/1 برابر فشار طراحي و يا مساوي با MAWP در نظر گرفته ميشود .
ماکزيمم تنش مجاز ( UG-23 ) : مقدار اين کميت بستگي به جنس ماده بکار رفته در ساخت مخزن داشته و مستقيما با خواص مکانيکي ماده تشکيل دهنده مخزن در ارتباط است .
انتخاب مواد :
يکي از مهمترين مسائل در طراحي مخازن تحت فشار انتخاب صحيح مواد اوليه بکار رفته در آنها مي باشد چرا که اين امر تاثير به سزائي در تعيين ضخامتها، ابعاد و نهايتا شرايط عملکردي مخزن دارد . اطلاعات مهم براي انتخاب مناسب مواد شامل تعيين مشخصه ها و مقادير ( و تغييرات تاثير گذار) سيال در اجزاء مختلف مخزن مي گردد .
کنترل ورق هاي ورودي:
هر ورقي که توليد مي شود بايستي از شرکت توليد کننده آن يک گواهي نامه داشته باشد . در اين گواهينامه يکسري اطلاعات مربوط به ورق درج شده است هر ورقي يک Heat number دارد که از طريق اين Heat Number مي توان ورق را رديابي کرد و يک سري اطلاعات مربوط به ورق را از جمله خواص مکانيکي و ترکيبات شيميايي و . . . بدست آورد بعضي مواقع در کارخانه يک سري ورق وارد مي شود که داراي Heat Number نيستند و يا به عبارتي پاک شده اند يا قابل ديدن نيستند . در حالت ايده آل کارخانه يک تيکه از ورق مورد نظر را بريده و به آزمايشگاه مي دهد . تا يک سري آزمايشات و تست هايي روي ورق انجام گيرد بعد از دريافت جواب آزمايشگاه پارامترهايي که آزمايشگاه بدست آورده را با پارامترهاي موجود در گواهينامه ورق ها مقايسه مي کنيم تا ببينيم حدس ما در مورد آن ورقي که مي خواستيم درست است يا نه .
به طور مثال ما سفارش ورق A516 Gr70 داديم و ورق هاي دريافتي هيچ گونه Heat Number ندارد براي صحت کار خود مراحل بالا را بايستي انجام دهيم .
وپارامترهايي که در کنترل ورق بايستي توجه شوديکي تميزي ورق، ضخامت ورق مي باشدکه ضخامت ورق ها رامعمولاً باکوليس اندازه مي گيرند.
کنترل لوله هاي ورودي :
لوله ها مانند ورق ها نيز داراي يک سري مشخصات فني مانند Heat Number و Schedule و قطر ( سايز لوله) و جنس لوله مي باشد که معمولاً Heat Number ها در ابتدا و انتهاي لوله ها درج مي شود .
Schedule : به عبارت عاميانه به گوشت لوله و يا ضخامت ديواره هاي لوله معروف مي باشد .
Scheduleها متنوع مي باشند که مي توانند
SCH (10,20,30,40,60,80,100,120,140,160)
يک سري جداول وجود دارند که با فرض معلوم بون سايز لوله و Schedule آن مي توان ضخامت ديواره لوله را از روي جداول بدست آورد . اطلاعات بدست آمده از جدول را با اطلاعاتي که خود با اندازه گيري ديواره لوله با کوليس انجام داديم مقايسه کرد .تا مطمئن شويم که لوله مورد نظر درست است .
کنترل فلنج ها و زانويي ها و ديگر اتصالات ورودي به کارخانه :
مأمور کنترل کيفيت با داشتن درخواست سفارش کارخانه براي کنترل اتصالات اقدام مي کند هر يک از اتصالات ورودي به کارخانه داراي يک سري مشخصات است که روي اتصالات حک شده است وظيفه مأمور چک کردن کالاي ورودي کارخانه با دستور سفارش مي باشد و بعد از چک کردن تحويل انباردار کارخانه مي دهد .
ابعاد و اندازه ورق ها :
معمولاً ورق هاي استاندارد ايراني به طول 6 متر و عرض 1.5 متر مي باشد در صورتيکه ورق هاي خاري به طول 6 متر و عرض 2 متر مي باشد معمولاً ورق هايي که توليد شده اند به همان اندازه واقعي که گفته شده نيستند معمولاً 10 الي 15 ميليمتر بزرگتر از اندازه اسمي مي باشد .
پارامترهاي کنترل ورق هاي بريده شده :
بعد از بريدن ورق ها به اندازه هاي محاسبه شده بايستي مجدداً توسط مإمور کنترل کيفيت اين ورق ها اندازه گيري و بعد با گونيا از قائمه بودن و صاف بريده شدن ورق ها اطمينان حاصل شود .
پارامترهاي اندازه گيري شامل طول و عرض و قطر آن مستطيل مي باشد .
اندازه گيري قطر به منظور اين است که ورق ما مستطيل بريده شود يا به عبارتي اطمينان از صاف بريده شدن عرض ورق . قطرهاي مستطيل مي توانند تا 3 سانتيمتر تلرانس داشته باشند .
بعد از تأييد از درست بودن اندازه ها، ورق ها را به قسمت نورد (رول کردن) منتقل مي کنند .
در قسمت نورد با باردهي توسط دستگاه نورد ورق را رول ميکند و در بيشتر ورق خود را مي اندازد .
بعد از رول کردن ورق بايستي ورق رول شده جوش شود . هر جوشي که روي ورق ها صورت مي گيرد بايستي مطابق با WPS باشد که ممکن است الکترود دستي يا جوش زير پودري باشد .
پس از جوش دادن ورق هاي رول شده بايستي قطر اين ورق ها توسط مأمور کنترل کيفيت اندازه گيري شود معمولاً بايستي 4 قطر و دو محيط خارجي شل ها اندازه گيري شود. در اندازه گيري قطرها معيار براي ما اندازه بزرگتر مي باشد .
در اندازه گيري قطرها معمولاً يک قطر بزرگ و يک قطر کوچک بدست مي آيد .
پس از اين مرحله نوبت به مونتاژ شل ها به هم مي شود . در نقشه ساخت زاويه بين خط جوش ها داده شده است به عبارتي هر شل داراي يک خط جوش طولي مي باشد هنگامي که دوشل به هم مونتاژ مي شود بايستي خط جوش هاي طولي آنها مطابق با نقشه قرار گرفته باشد .
براي محاسبه زاويه بين دو خط جوش که در نقشه آمده به ميليمتر بايستي به اين صورت عمل کرد که مطابق نقشه محيط خارجي شل ها را اندازه گرفته در زاويه مورد نظر ضرب کرده و بعد به 360تقسيم مي کند تا زاويه مورد نظر بر حسب ميليمتر بدست آيد .
بعد از مونتاژ شل ها بايستي مطابق با WPS شل ها به هم جوش شوند . ابتدا از داخل با جوش الکترود دستي يک پاس ريشه مي زنند و بعد از بيرون شل قسمت جوش شده را سنگ مي زنند تا ريشه جوش کاملا مشخص شود بعد روي ريشه جوش تست PT انجام مي گيرد . بعد از انجام تست PT از سالم بودن جوش اطمينان حاصل شد شروع به جوشکاري از بيرون مي کنيم که مي تواند جوش الکترود دستي يا زير پودري باشد . بعد از اين که شل ها کاملاً جوش خوردن بايستي تست راديوگرافي ياالتراسونيک روي آنها انجام گيرد .
مونتاژ شل به Head :
معمولاً ضخامت Head را بزرگتر يا حداقل برابر با ضخامت ورق شل در نظر ميگيرند و بعد توسط نوعي گيج مخصوصي بايستي از هالويي نداشتن به سمت داخل اطمينان حاصل گردد . معمولاً اختلاف ضخامت را به بيرون شل مي اندازند داخل شل بايستي کاملاً هم امتداد هم باشد .
طريقه محور بندي کردن مخزن ( اکس بندي کردن):
بعد از اينکه شل ها به هم مونتاژ شد مطابق نقشه معمولاً سوراخ manhole ( opening) در زاويه 180 درجه يا 90 درجه با خط محور مخزن قرار دارد . پس ابتدا بايستي از روي نقشه زاويه خط جوش طولي نزديک به manhole را از نقشه بر حسب زاويه داده شده است را تبديل به ميليمتر کرده و بر روي شل با سنبه زدن ايجاد کنيم و بعد توسط هوا برش دايره اي مطابق با نقشه به روي شل ايجاد مي کنيم .
در واقع همانطور که گفته شد معمولاً manhole در زاويه 90, 180 و 270 قرار دارد . از روي همان خط سنبه محيط را به چهار قسمت مساوي تقسيم مي کنيم و بعد از تقسيم محيط توسط خط کشي خط محور را در طول مخزن امتداد و اين کار را در هر چهار طرف مخزن انجام مي دهيم . اين خطوط محور بطور عاميانه به خطوط آکس معروف مي باشد .
دليل آکس بندي کردن مخزن بخاطر مونتاژ نازل ها و اتصالاتي است که روي مخزن سوار مي شوند چون مطابق با نقشه اندازه نازل ها را تا خط اکس مخزن مي دهند که به projection معروف است .
قبل از هر گونه مونتاژ نازل بايستي از تراز بودن خود مخزن اطمينان حاصل کرد . معمولاً براي تراز کردن مخزن از شيلنگ تراز استفاده مي کنند شيلنگ تراز شيلنگي است که درون آن به ميزان مشخصي آب وجود دارد فقط بايستي در هنگام پر کردن آب در داخل شيلنگ مراقب باشيم که هوا داخل شيلنگ وجود نداشته باشد چون هواي موجود در آب باعث مي شود که معيار تراز بودن ما صحيح نگردد
و در نهايت تست NDTباتوجه به جدول زير انجام ميگردد و در پرونده مخزن بايگاني گردد
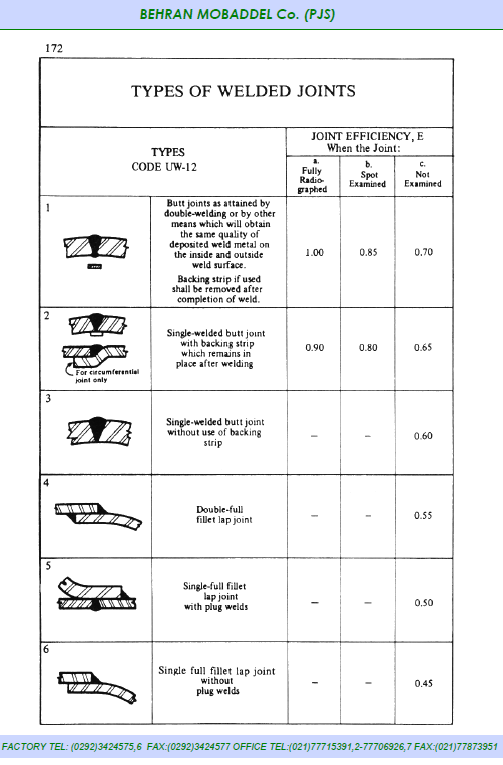
استحکام اتصالات ( UW-12 ) : مقداراين پارامتر (E ) بستگي به نحوه اتصالات و درصد راديوگرافي آنها دارد . در مورد مخزني که قرار است بطور کامل راديوگرافي شود ( فشار طراحي بالاتر از psi براي بويلر بخار، حاوي مواد سمي و يا ضخامت بيشتر از براي C.S و براي S.S ) ، لازم است تا کليه خطوط A و D بصورت صد در صد و خطوط C و B ( به شرط اينکه از لوله 10in و يا ضخامت فراتر رفته باشد ) راديوگرافي شوند . اما اگر قرار باشد که مخزني بصورت موضعي راديوگرافي شود ، آنگاه محلهاي اتصال خطوط B و C با خطوط دسته A ( شامل نازلهاي با قطر بيش از از 10 in و ضخامت 1in ) و محل تماس مقاطع بدون درز مخزن يا عدسي ها وقتيکه طراحي جوشهاي A و D بر مبناي استحکام 1. يا 0.9 صورت ميپذيرد ، بايد بطور موضعي راديوگرافي شوند .
چنانچه مخزني فاقد هرگونه راديوگرافي طراحي شده باشد آنگاه بايد حائز يکي از شرايط زير باشد :
الف – تنها فشار خارجي وجود داشته باشد .
ب- طراحي اتصالات بدون در نظر گرفتن تست راديوگرافي صورت پذيرفته باشد .
طراحي SHELL و (UG-27 , 28 , 32, 33, ) HEAD :
با توجه به روابط موجود ( از مقاومت مصالح) در رابطه با محاسبه ضخامت مورد نياز جهت پوسته و عدسي يک مخزن تحت فشار استوانه اي شکل , مي توان از روابط زير بهره گرفت :
که در آنها :
t : Shell Thickness (in)
p : Pressure (psi)
R : Internal Radius
S : Stress Value (psi)
E : Joint Efficiency
.
طريقه استفاده از شيلنگ تراز :
لبه شيلنگ را روي ابتدا محور در ابتدا مخزن قرار مي دهيم و بعد انتهاي شيلنگ را در انتهاي محور در انتهاي مخزن قرار مي دهيم بايستي آب موجود در شيلنگ دقيقاً روي خط محور در ابتدا و انتها قرار گيرد اگر اين طور شد که مخزن تراز است و اگر اين طور نبود که مخزن تراز نيست بايستي تراز شود.
اين کار را معمولاً در دو يا سه طرف مخزن بطور قطري يا عرضي و يا طولي انجام مي دهند که کاملاً از تراز بودن مخزن اطمينان حاصل شود .
نازل: نازل ترکيبي از فلنج و لوله است که هر دو آنها در هنگام مونتاژ بايستي داراي يک مشخصات باشد مثلاً از يک Schedule باشند .
از آنجايي که Schedule فلنج با Schedule لوله يکي است بعضي مواقع پيش مي آيد که يک ميزان مشخصي از لحاظ ضخامت اختلاف داشته باشند در اين مواقع بايستي به نسبت 3 به 1 فلنج يا لوله را tapere زد .
در هنگام مونتاژ نازل ها بايستي يکسري مراحل را رعايت کرد از جمله فاصله معيني بين لوله و فلنج در نظر گرفته شود (GAP ) و بعد توسط گونيا از مونتاژ شدن فلنج به لوله اطمينان حاصل شود و بعد توسط مامور کنترل کيفيت بازديد شود . و مامور کنترل کيفيت با داشتن گيج مخصوصي از هم امتداد بودن لوله و فلنج در يک راستا اطمينان حاصل کند و بعد مطابق با WPS که دارد نازل هاي مونتاژ شده جوش مي شوند که معمولاٌ پاس ريشه در نازل ها با جوش آرگن و پاس هاي بعدي با الکترود E7018 صورت مي گيرد و بعد از جوش مجدداً مامور کنترل کيفيت توسط چراغي از لحاظ چشمي جوش داخل و لوله را بازديد مي کند تا اطمينان حاصل که جوش کاملاً نفوذ کرده و يا بدون هيچ گونه شورگي باشد . پس از تاييد از لحاظ چشمي بسته به نوع نازل تست غيره مخرب مي شود که معمولاً RT است
انواع فلنج ها :
1- welding Neck
2- Slip on
3- Long welding Neck
4- Blind
نکته : براي فلنج welding Neck نياز به تسهاي RT و VT مي باشد .
نکته : براي فلنج Slip on نياز به تسهاي PT وVT مي باشد .
نکته : براي فلنج Long welding neck نيازي به تست نمي باشد .
نکته : فلنج Blind براي کور کردن فلنج استفاده مي شود .
مونتاژ کردن نازل به شل :
هر نازل مطابق با نقشه معمولاً در يک زاويه و در يک فاصله مشخصي از خط آکس قرار دارد . معمولاً در هنگام مونتاژ نازل به شل به اندازه 2 ميليمتر يا بيشتر بر اساس سايز فلنج ارتفاع نازل را تا خط آکس بيشتر مي گيرند اين mm2 را به عنوان اينکه جوش خود را مي کشد مي باشد.
در هنگام مونتاژ نازل به شل ابتدا بايستي از تراز بودن مخزن اطمينان داشته باشيم بعد توسط يک شمشه و يک تراز از تراز بودن و همچنين توسط يک ريسمان يا به عبارتي شاقول خط اکس فلنج نازل را در امتداد خط آکس مخزن کنترل مي کنيم و بعد ارتفاع از Face فلنج را از دو طرف فلنج تا شل اندازه گرفته و از مساوي بودن آن اطمينان حاصل مي کنيم . و بعد مطابق با WPS که دارد آن را جوش مي دهند .
لازم به ذکر است که projection هر نازلي با نازل ديگر مي تواند از لحاظ موقعيت فرق داشته باشد که بايستي به نقشه مراجعه شود .
تستي که در هنگام جوش نازل به شل بايستي انجام شود UT مي باشد که معمولاً تست UT و RT خود کارخانه انجام نمي داد بلکه از بيرون افرادي مي آمدند و اين کار را انجام مي دادند و يکسري نازل ها داراي pad مي باشند و يکسري ها هم بدون Pad به شل مونتاژ مي شدند معمولاً تستي که روي Pad دور نازل ها صورت مي گيرد تست PT مي باشد .
Saddle يا پايه مخزن:
پايه مخزن معمولاً بر اساس حجم و وزن مخازن و تنش هايي که از مخزن به آن اعمال مي شود طراحي مي شود . تمام جوش هايي که در پايه بکار مي رود جوش گوشه است و تستي که بايستي روي آن انجام گيرد تست PT و VT است به عبارتي هر جا که جوش گوشه در مخزن داشته باشيم بايستي تست PT روي آن انجام گيرد.
عدسي يا Head :
عدسي ها انواع مختلفي دارند از جمله بيضوي , کروي , تخت , مخروطي .
SPHERE and HEMISPHERICAL HEAD
ELLIPSOIDAL HEAD
FLAT HEADS
پارامترهايي که بايستي در اندازه گيري يک عدسي رعايت شود :
1- عمق يا ارتفاع عدسي
2- اندازه قسمت صاف يا راست عدسي
3- معمولاً هر عدسي شامل 4 ناحيه يا به عبارتي داراي 4 شعاع مي باشد که بايستي کنترل شود
4- ضخامت اين چهار ناحيه بايستي توسط ضخامت سنج اندازه گيري شود و نبايستي اين ضخامت ها از ضخامت ورق شل کمتر باشد .
براي کنترل عدسي ها به صورت صحيح معمولاً از يک شابلون که در کارخانه ساخته شده است استفاده مي کنند .
تست هيدرواستاتيک :
بعد از اينکه همه مراحل ساخت مخزن انجام گرفت نوبت به تست هيدرواستاتيک مي رسد که فشاري در حدود 5/1 برابر فشار طراحي بايد به به مخزن اعمال کرد .
رنگ آميزي : کليه سطوح ماشينکاري شده مانند سطح فلنج ها، اتصالات رزوه اي با پوشش يا درپوش مناسب پوشانده شود.
کليه مجراهاي باز به داخل مخزن با درپوش مناسب پوشانده شود.
سوراخ هايي که بر روي ورق هاي تقويتي تعبيه شده مي بايست توسط موادي نظير گريس پر شوند.
جهت اعمال عمليات سندبلاست 4 سطح مطابق با استاندارد سوئدي جهت سندبلاست موجود است که به قرار ذيل مي باشند:Sa1-Sa2-Sa2.1/2-Sa3
-بمنظور بررسي چسبندگي مناسب رنگ مي توان از استانداردهاي مربوطه از جملهASTM D3359 ( تست شطرنجي) استفاده نمود.
-بمنظور اطمينان از درستي ضخامت لايه رنگ اعمالي از ضخامت سنجي در مراحل تر و خشک استفاده ميشود.